ER347SI
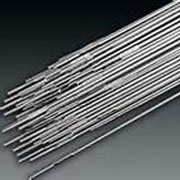
Class: ER347Si
AWS: A5.9
Conforms to Certification: AWS A5.9 | ASME SFA A5.9
Weld Process Used for Tig: (GTAW)
AWS Chemical Composition Requirements
C = 0.08 max
Cr = 19.0 – 21.5
Ni = 9.0 – 11.0
Mo = 0.75 max
Mn = 1.0 – 2.5
Si = 0.65 – 1.00
P = 0.03 max
S = 0.03 max
Cu = 0.75 max
Nb = 10 x C (min) – 1.0 (max)
Available Sizes
.030 x 36
.035 x 36
.045 x 36
1/16 x 36
3/32 x 36
1/8 x 36
3/16 x 36
5/32 x 36
Application
ER347SI is a columbium stabilized stainless steel welding wire used to weld Types 321 and 347. Addition of columbium reduces the possibility of chromium carbide precipitation and consequent inter-granular corrosion. ER347SI is recommended if the weld metal is to be subjected to high temperatures above 750ºF.
Deposited Chemical Composition % (Typical) | ||
C = 0.04 | Mo = 0.30 | P = 0.025 |
Cr = 20.00 | Mn = 1.50 | S = 0.015 |
Ni = 9.50 | Si = 0.80 | Cu = 0.10 |
Nb = 0.40 |
Mechanical Properties (R.T.) | |
Yield Strength | 88,000psi |
Tensile Strength | 58,000psi |
Elongation | 42% |
Deposited All Weld Metal Properties
Data is typical for ER347SI weld metal deposited by Tig using 100% Argon as the shielding gas.
Recommended Welding Parameters |
|||
GTAW “Tig Process” | |||
Wire Diameter | Amps DCSP | Volts | Shielding Gas |
.035 | 60-90 | 12-15 | Argon 100% |
.045 | 80-110 | 13-16 | Argon 100% |
1/16 | 90-130 | 14-16 | Argon 100% |
3/32 | 120-175 | 15-20 | Argon 100% |
Note: Parameters for tig welding are dependent upon plate thickness and welding position.
Other shielding Gases may be used for Tig welding. Shielding gases are chosen taking Quality, Cost, and Operability into consideration.