ERNi-CI
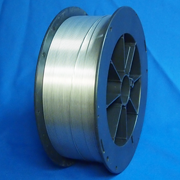
Class: ERNi-CI
AWS: A5.15
Conforms to Certification: AWS A5.15 | ASME SFA A5.15
Weld Process: GMAW & SAW Welding Processes
AWS Chemical Composition Requirements | |
C = 0.1 max | Si = 0.10 max |
Mn = 0.30 max | Cu = 0.20 max |
Fe = 0.20 max | Ni = 99.2 min |
S = 0.01 max | P = 0.01 max |
Available Sizes |
|
Diameter X Spool Sizes | Diameter X Coil Sizes |
.035 x 33# | 1/16 x COIL |
.045 x 33# | 3/32 x COIL |
1/16 x 33# | 1/8 x COIL |
5/32 x COIL |
Application
ERNi-CI Nickel Alloy 99 classification is used for tig and mig welding of cast irons. Major use is the repair of gray iron castings. The welds are easy to machine.
Deposited Chemical Composition % (Typical) | ||
C = 0.01 | S = 0.002 | Ni = 99.62 |
Mn = 0.17 | Cu = 0.13 | Fe = 0.01 |
Si = 0.05 | P = 0.001 |
Deposited All Weld Metal Properties % (AW) | |
Tensile Strength | 70,000 psi |
Yield Strength | 36,000 psi |
Elongation | 40% |
Deposited Charpy-V-Notch Impact Properties %
Not applicable
Recommended Welding Parameters for MIG and SAW Welding of Nickel Alloys | ||||
Process | Diameter of Wire | Voltage (V) | Amperage (A) | Gas |
MIG | .035 inches | 26 – 29 | 150 – 190 | 75 % Argon +25% Helium |
.045 inches | 28 – 32 | 180 – 220 | 75 % Argon +25% Helium | |
1/16 inches | 29 – 33 | 200 – 250 | 75 % Argon +25% Helium | |
SAW | 3/32 inches | 28 – 30 | 270 – 350 | Suitable Flux May Be Used. |
1/8 inches | 29 – 32 | 350 – 450 | Suitable Flux May Be Used. | |
5/32 inches | 30 – 33 | 400 – 550 | Suitable Flux May Be Used. |
Note: Other shielding Gases may be used for Mig welding. Shielding gases are chosen taking Quality, cost, and Operability into consideration.
Note: Both agglomerated and fused fluxes can be used for submerged arc welding.
Note: The chemical composition of the flux mainly affects the chemistry of the weld metal and consequently its corrosion resistance and mechanical properties.