Cobalt #6 CTD Electrode
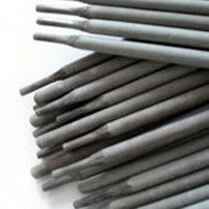
Class: ECoCr-A
AWS: A5.13
DURAMAX COBALT #6 CTD ELECTRODE
Conforms to Certification: AWS A5.13 | ASME SFA 5.13
Weld Process: Shielded Metal Arc
AWS Chemical Composition Requirements | ||
C = 0.7 – 1.4 | Mn = 2.0 max | Si = 2.0 max |
Cr = 25 – 32 | Ni = 3.0 max | Mo = 1.0 max |
Fe = 5.0 max | W = 3.0 – 6.0 | Co = Remainder |
Other = 1.0 max |
Product Description:
DURAMAX Cobalt#6 SMAW electrodes are our most popular and useful cobalt alloy, it offers an excellent balance between impact, heat, corrosion and metal-to-metal abrasion resistance. It also offers outstanding anti-galling properties, superior high temperature hardness and resistance to cavitation erosion making it perfect to use as valve trim in steam engines or repairing worn machine parts. DMCobalt#6 is ideal for many hard-surfacing applications because of its resistance to mechanical and chemical degradation at extreme temperature produces a medium hardness cobalt-chromium deposit for high temperature applications with good abrasive wear and good impact resistance. It bonds well with all weldable steels, including stainless.
Typical Applications: |
|||
– Hot Trimming Dies | – Chain Saw Bars | – Hot Punches | |
– Hot Oil Pump Parts | – Agitators | – Drawing Blocks | |
– High Pressure-High Temperature Valves | – Extruder Screws | ||
Deposited Chemical Compositon % (Typical) | |||
C = 1.1 | Mn = 0.9 | Si = 1.0 | |
Cr = 27.3 | Ni = 2.5 | Mo = 0.1 | |
Fe = 3.3 | W = 4.6 | Co = Balance | |
Typical Deposit Characteristics: |
|||
– Abrasion Resistance | Excellent | – Hardness | HRC 23 – 47 |
– Impact Resistance | Good | – Hot Weld Hardness | Excellent |
– Corrosion Resistance | Good | – Deposit layers | 2 Layers Max |
– Magnetic | No | – Deposit Cross Check | Not with proper preheat |
– Machineability | Carbide tools | – Proper Heat Treatment | & Slow Cooling |
Recommended Operation of Welding Rods
Flat Welding
Diameter | Amps DCEP |
1/8 | 90 – 120 |
5/32 | 145 – 165 |
3/16 | 175 – 195 |